Powerflex 700 Manual Fault Codes
View and Download Allen-Bradley Powerflex 700 user manual online. Free download movies. And/or electrical codes. Version Clr Fault Queue PowerFlex 700 Drive Alarm 1. View and Download Allen-Bradley Powerflex 700 user manual online. And/or electrical codes. Version Clr Fault Queue PowerFlex 700 Drive Alarm 1.
• Chapter 1 Programming and Parameters Parameter Name & Description Values page 16 for symbol descriptions 132 [PI Upper Limit] Default: +[Maximum Freq] 100% Sets the upper limit of the PI output. Min/Max: –/+400.0 Hz –/+800.0% Units: 0.1 Hz 0.1% 133 [PI Preload] Default: 0.0 Hz. • Programming and Parameters Chapter 1 Parameter Name & Description Values page 16 for symbol descriptions 445 [Ki Speed Loop] Default: Controls the integral error gain of the speed Min/Max: 0.0/4000.0 regulator.
Powerflex 700 Installation Manual
The Vector Control option provides the added capability of FVC Vector control. • Programming and Parameters Basic Parameter View – Standard Control Option Parameter 196 [Param Access Lvl] set to option 0 “Basic.” File Group Parameters Monitor Metering Output Freq Commanded Freq 002 Output Current M o n it DC Bus Voltage Motor Control Motor Data Motor NP Volts Motor NP RPM. • Programming and Parameters Basic Parameter View – Vector Control Option Parameter 196 [Param Access Lvl] set to option 0 “Basic.” File Group Parameters Monitor Metering Output Freq Commanded Speed002 Commanded Torque**024 M o n it Output Current Torque Current DC Bus Voltage Motor Control Motor Data Motor NP Volts. • Programming and Parameters Advanced Parameter View – Standard Control Option Parameter 196 [Param Access Lvl] set to option 1 “Advanced.” File Group Parameters Monitor Metering Output Freq Output Voltage MOP Frequency Commanded Freq 002 Output Power DC Bus Voltage Output Current Output Powr Fctr 008 DC Bus Memory 013 M o n it. • Programming and Parameters File Group Parameters Utility Direction Config Direction Mode HIM Ref Config Save HIM Ref U ti li ty Man Ref Preload 193 MOP Config Save MOP Ref MOP Rate Drive Memory Param Access Lvl 196 Save To User Set 199 Voltage Class Reset To Defalts 197 Reset Meters. • Programming and Parameters Advanced Parameter View – Vector Control Option Parameter 196 [Param Access Lvl] set to option 1 “Advanced.” File Group Parameters Monitor Metering Output Freq Torque Current MOP Reference Commanded Speed 002 Flux Current DC Bus Voltage Ramped Speed Output Voltage DC Bus Memory 013 M o n it.
• Chapter 1 Programming and Parameters Parameter Name & Description Values page 16 for symbol descriptions 299 [DPI Fdbk Select] Default: “Speed Fdbk” Selects the DPI units displayed on the first line of Options: “Output Freq” the HIM and the feedback word through any “Command Spd”. • Programming and Parameters Chapter 1 Parameter Name & Description Values page 16 for symbol descriptions 284 [MOP Mask] [Logic Mask].
• 3-32 Programming and Parameters Parameter Name & Description Values page 3-2 for symbol descriptions [Droop RPM @ FLA] Default: 0.0 RPM Vector Selects amount of droop that the speed Min/Max: 0.0/200.0 RPM reference is reduced when at full load Units: 0.1 RPM torque. • Programming and Parameters 3-33 Parameter Name & Description Values page 3-2 for symbol descriptions 158 [DC Brake Level] Default: [Rated Amps] 0/[Rated Amps] × 1.5 Defines the DC brake current level Min/Max: injected into the motor when “DC Brake” (Equation yields is selected as a stop mode. • 3-34 Programming and Parameters Parameter Name & Description Values page 3-2 for symbol descriptions 163 [DB Resistor Type] Default: “Internal Res” “None” Vector Selects whether the internal or an external DB resistor will be used. Options: “Internal Res” “External Res” Important: In 0-3 Frame drives, only one “None”. • Programming and Parameters 3-35 Parameter Name & Description Values page 3-2 for symbol descriptions 169 [Flying Start En] Default: “Disabled” Enables/disables the function which Options: “Disabled” reconnects to a spinning motor at actual “Enabled” RPM when a start command is issued. Not required in FVC Vector mode when using an encoder.
Powerflex 700 Manual Fault Codes
Drive, Comm Card, EN2T Cards? We just had an issue with communications being lost between our PLC's and main plant network because of firmware issues with the brand new EN2T cards (like fresh out of the box by a couple of weeks new).
➂ 85% of nominal for longer than [Power Loss Time]. Enable/ Disable with [Fault Config 1] on page 3-46.
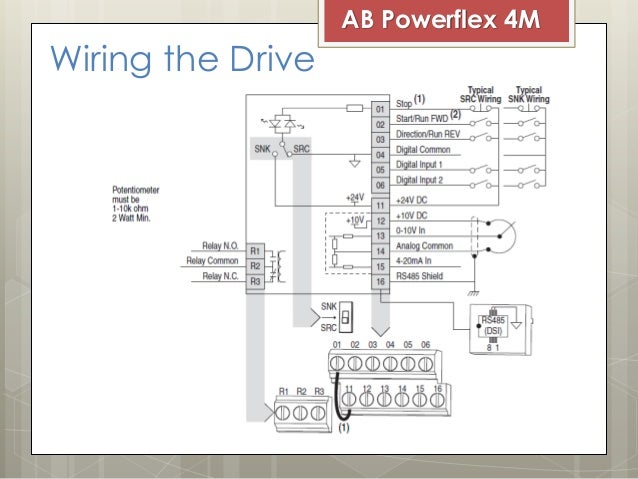
• Installation/Wiring Fuses and Circuit Breakers The PowerFlex 700 can be installed with either input fuses or an input circuit breaker. National and local industrial safety regulations and/or electrical codes may determine additional requirements for these installations. Refer to Appendix A for recommended fuses/circuit breakers. • Installation/Wiring Shielded/Armored Cable Shielded cable contains all of the general benefits of multi-conductor cable with the added benefit of a copper braided shield that can contain much of the noise generated by a typical AC Drive. Strong consideration for shielded cable should be given in installations with sensitive equipment such as weigh scales, capacitive proximity switches and other devices that may be affected by electrical noise in the distribution system.
• ATTENTION: The following information is merely a guide for proper installation. The Allen-Bradley Company cannot assume responsibility for the compliance or the noncompliance to any code, national, local or otherwise for the proper installation of this drive or associated equipment. • Installation/Wiring Mounting Considerations Operating Temperatures PowerFlex 700 drives are designed to operate at 0° to 40° C ambient. To operate the drive in installations between 41° and 50° C, see below.
• 3-56 Programming and Parameters Parameter Name & Description Values page 3-2 for symbol descriptions [Anlg Out1 Scale] Default: Vector v3 [Anlg Out2 Scale] Vector v3 Min/Max: [Analog Out1 Sel] Sets the high value for the range of Units: 0.01 analog out scale. Entering 0.0 will disable this scale and max scale will be used. • Programming and Parameters 3-57 Parameter Name & Description Values page 3-2 for symbol descriptions [Digital In1 Sel] Default: “Stop – CF” [Digital In2 Sel] Default: “Start” [Digital In3 Sel] Default: “Auto/ Manual” [Digital In4 Sel] Default: “Speed Sel 1” [Digital In5 Sel] Default: “Speed Sel 2”.
• C-14 Application Notes It can operate as trim mode by summing the PI loop output with a master speed reference. Slip Comp Slip Adder Open Loop Linear Ramp Spd Ref Spd Cmd & S-Curve Process PI Ref Process PI Controller PI Fbk PI Enabled Speed Control. • Application Notes C-15 If no digital input is configured to “PI Enable,” then only the Bit 0 = 1 condition must be met. If the bit is permanently set to a “1”, then the loop will become enabled as soon as the drive goes into “run”.
The shape of the V/Hz curve can be controlled a limited amount, but once the shape is determined, the drive output is fixed to those values. • 0.5% because they do not have connections for a feedback device. The PowerFlex 700 with the Vector Control option can offer better speed regulation by adding speed feedback. Using a speed feedback device (encoder) tightens speed regulation to 0.001% of base speed and extends.
• Programming and Parameters Chapter 1 Parameter Name & Description Values page 16 for symbol descriptions 229 [Alarm 1 @ Fault] Read Only Captures and displays [Drive Alarm 1] at the time of the last fault. 1 = Condition True 0 = Condition False x = Reserved Bit #. • Chapter 1 Programming and Parameters Parameter Name & Description Values page 16 for symbol descriptions 238 [Fault Config 1] Enables/disables annunciation of the listed faults. 1 = Enabled 0 = Disabled x = Reserved Bit # Factory Default Bit Values 1 = Enabled 0 = Disabled x = Reserved. • Programming and Parameters Chapter 1 Parameter Name & Description Values page 16 for symbol descriptions [Fault 1 Time] Default: Read Only [Fault 2 Time] Min/Max: 0.0000/2 Hr [Fault 3 Time] Units: 0.0001 Hr [Fault 4 Time] [Fault 5 Time] [Fault 6 Time] [Fault 7 Time] [Fault 8 Time] The time between initial drive power up and the occurrence of the associated trip fault. • Chapter 1 Programming and Parameters Parameter Name & Description Values page 16 for symbol descriptions [Alarm 1 Code] Default: Read Only [Alarm 2 Code] Min/Max: 0/65535 [Alarm 3 Code] Units: [Alarm 4 Code] [Alarm 5 Code] [Alarm 6 Code] [Alarm 7 Code] [Alarm 8 Code] A code that represents a drive alarm.
• Programming and Parameters Chapter 1 Parameter Name & Description Values page 16 for symbol descriptions 670 [Adj Volt Trim Hi] 100.0% Default: Scales the upper value of the [Adj Volt TrimSel] Min/Max: 0.0/100.0% of Drive Rated Volts selection when the source is an analog input. Units: 0.1% 671 [Adj Volt Trim Lo]. • Chapter 1 Programming and Parameters Pos/Spd Profile File Parameter Name & Description Values page 16 for symbol descriptions 700 [Pos/Spd Prof Sts] Read Only Provides status of the profile/indexer. Bits 0-4 are a binary value.
[Sleep-Wake Ref] must be set to the analog input that will control 'Start/Stop' functions. Meet all Conditions! [Sleep-Wake Mode] must = '1, Direct' (Enable) or '2, Invert (Enable).' • Application Notes C-21 Start At PowerUp Standard Control Option When Start At Powerup in 2 wire control is configured, the drive will start if the start permissive conditions are met within 10 seconds of drive power being applied. An alarm will be annunciated from application of power until the drive actually starts, indicating the powerup start attempt is in progress.
Refer to Appendix A for recommended fuses/circuit breakers. • Installation/Wiring Shielded/Armored Cable Shielded cable contains all of the general benefits of multi-conductor cable with the added benefit of a copper braided shield that can contain much of the noise generated by a typical AC Drive. Strong consideration for shielded cable should be given in installations with sensitive equipment such as weigh scales, capacitive proximity switches and other devices that may be affected by electrical noise in the distribution system. • Installation/Wiring Location Rating/Type Description • Three tinned copper conductors with XLPE insulation. Standard Tray rated 600V, 90° C • 5 mil single helical copper tape (25% overlap min.) with (Option 2) (194° F) RHH/RHW-2 Anixter OLF-7xxxxx or three bare copper grounds in contact with shield.
Choices are dynamic brake, “Adjust Freq”. • Programming and Parameters Chapter 1 Parameter Name & Description Values page 16 for symbol descriptions 167 [Powerup Delay] Default: 0.0 Secs Defines the programmed delay time, in seconds, Min/Max: 0.0/10800.0 Secs before a start command is accepted after a power Units: 0.1 Secs 168 [Start At PowerUp]. • Chapter 1 Programming and Parameters Parameter Name & Description Values page 16 for symbol descriptions 178 [Sleep-Wake Mode] Default: “Disabled” Enables/disables the Sleep/Wake function. Options: “Disabled” Important: When enabled, the following “Direct” (Enabled) conditions must be met: “Invert” (Enabled) • A proper value must be programmed for [Sleep Level] &. • Programming and Parameters Chapter 1 Parameter Name & Description Values page 16 for symbol descriptions 182 [Sleep Level] Default: 5.000 mA, 5.000 Volts Defines the analog input level that will stop the Min/Max: 4.000 mA/[Wake Level] drive. 0.000 Volts/[Wake Level] Units: 0.001 mA 0.001 Volts. • Chapter 1 Programming and Parameters Utility File Parameter Name & Description Values page 16 for symbol descriptions 190 [Direction Mode] Default: “Unipolar” Selects method for changing direction.
Comments are closed.